Why does it take so long?
26/04/2023
So many different elements can affect hand building clay, even down to the weather!
I start with wet clay, wedging and rolling – generally prepping, as it starts to dry it becomes soft clay5, at this stage I can start cutting shapes, prepping joins, laying it over a former or use the *kurinuki (to carve from) technique.
Did you know clay has a ‘muscle memory’ and is inclined to warp when drying, if move too much at this stage. Leather hard clay, is still dark but structurally sound enough to join together with clay slip (liquid clay). In the summer in the UK when it is warm as thin piece of wet clay can become leather hard in an hour, in the winter it can take a day! You can slow this down by covering pieces as clay behaves better when it dries evenly. Smoothing at this stage is necessary; *scrafitto (to scrap away) can also be tried on leather hard clay; so can *burnishing (to rub - draws the water to the surface). Leaving it to become bone dry is crucial, at this stage your piece is most fragile, so many pieces that you have spent hours on, break at this stage, just take a deep breath and recycle it! When it is bone dry, fettling occurs (trimming & smoothing very carefully), or you can add underglaze at this stage or indeed to just beyond leather hard clay. Up until this point, our work is referred to as green ware.
Currently, I have to wrap everything at this stage and transport it to the kiln I hire. Wrapping it carefully is time consuming but essential, even carefully wrapped pieces sometimes don’t make it.
Potholes must be avoided at all costs! Sometimes, pieces can be re-joined if the two parts have the same ‘water’ content. Surviving bisque firing to 1000 degrees Celsius, transforms your piece into a more robust piece but still breakable. Bisque firing takes approximately 10 hours to fire and 10 hours to cool down! Wrapping and returning home is a little less scary drive.
Our bisque ware is now ready for applying glaze; this can be underglaze or high fire glaze. I apply this by hand, which means to get a true opaque colour you need to apply three coats, allowing each coat to dry in between. If I have used underglaze and want a glossy finish, I then have to apply 3 coats of clear high fire glaze which obliterates my hand painted work and you have to trust the magic/science of heat work! I do occasionally use dipping glaze, this is much quicker and usually involves a 3-5 second dip in a bucket of glaze. All glazing must be dry before I again have to wrap it all up, so as not to knock the fragile glaze surface off each piece and transport for glaze firing. This time the kiln is fired to 1220 degrees Celsius, and although hotter it is quicker as the clay has already been fired to 1000 degrees Celsius. The glaze fuses with the clay become ceramic ware, or functional stoneware; only taking about 8 hours in the kiln this time to reach temperature, but still 10 hours to cool down. Wrapped again then taken home. Process not quite finished. If it is a vessel, I perform a seep test to make sure they are water tight and if they are a jug, a pour test, hoping there are no drips! Then it is time to photograph and catalogue each piece. So not many stages then…Each piece is different, and the pricing reflects how long it takes at each stage.
Marks in the clay are a record of my day, evidence of hand building - not perfected by machines.
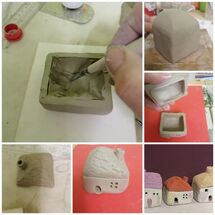
Collage 217-Kurinuki Style Cottages
Currently, I have to wrap everything at this stage and transport it to the kiln I hire. Wrapping it carefully is time consuming but essential, even carefully wrapped pieces sometimes don’t make it.
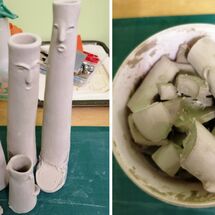
Bone dry pottery is very fragile
Our bisque ware is now ready for applying glaze; this can be underglaze or high fire glaze. I apply this by hand, which means to get a true opaque colour you need to apply three coats, allowing each coat to dry in between. If I have used underglaze and want a glossy finish, I then have to apply 3 coats of clear high fire glaze which obliterates my hand painted work and you have to trust the magic/science of heat work! I do occasionally use dipping glaze, this is much quicker and usually involves a 3-5 second dip in a bucket of glaze. All glazing must be dry before I again have to wrap it all up, so as not to knock the fragile glaze surface off each piece and transport for glaze firing. This time the kiln is fired to 1220 degrees Celsius, and although hotter it is quicker as the clay has already been fired to 1000 degrees Celsius. The glaze fuses with the clay become ceramic ware, or functional stoneware; only taking about 8 hours in the kiln this time to reach temperature, but still 10 hours to cool down. Wrapped again then taken home. Process not quite finished. If it is a vessel, I perform a seep test to make sure they are water tight and if they are a jug, a pour test, hoping there are no drips! Then it is time to photograph and catalogue each piece. So not many stages then…Each piece is different, and the pricing reflects how long it takes at each stage.
Marks in the clay are a record of my day, evidence of hand building - not perfected by machines.